Slurry Pump Spare parts Material
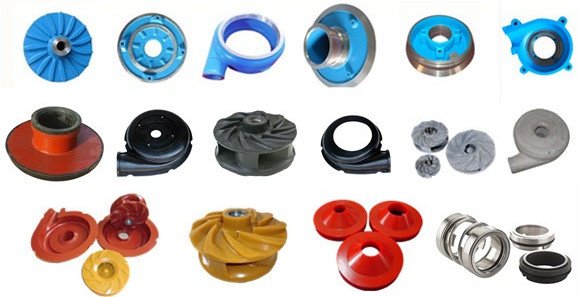
Slurry pumps used in metal materials, Including cast iron, ductile iron, high chromium cast iron, stainless steel duplex stainless steel etc. High chromium cast iron is the third generation of wear-resistant material developed after ordinary white cast iron and nickel hard cast iron. Due to the characteristics of the structure of high chromium cast iron, it has much higher toughness, higher temperature strength, heat resistance, and wear resistance than ordinary cast iron. High chromium cast iron has been praised as the best anti-abrasive material in the contemporary era, and it has been widely used day by day.
China’s national standard for wear-resistant white cast iron (GB/T8263) stipulates the grade, composition, hardness, heat treatment process, and usage characteristics of high chromium white cast iron.
WARMAN CODE | MATERIAL NAME | TYPE | DESCRIPTION |
A07 | 15/3 Chrome/Moly Iron | Chromium/ Molybdenum White Iron | Martensitic white iron with moderate erosion resistance. |
A12 | HYPERCHROMEÒ 30% Cr | Hypereutectic Chromium White Iron | HYPERCHROMEÒ alloy is a hypereutectic white iron suitable for high wear duties, where corrosion is not considered a problem. It should be used in applications where A05 and A04 do not provide an adequate wear life. Alloy A12 can be used in mild alkaline slurries, between a pH range of 8 to 14. The alloy may provide up to three times the wear life of A05 and A03 parts in some severe applications. |
A14 |
ULTRACHOME Tough 27% Cr |
Erosion Resistant White Iron | Alloy A14 is a high chromium white cast iron offering high impact resistance and moderate erosion wear resistance. Alloy A14 is suitable for gravel pump applications where large slurry particles are present. A14 is much tougher than A05 but also exhibits a lower erosion wear resistance. |
A25 | Ni – Cr – Mo Steel | Cast Steel | Alloy A25 is an alloy steel having moderate wear resistance and high mechanical properties. The alloy is used for large castings where toughness is of primary importance. |
A49 | ULTRACHOME 28% Cr, Low C | Low Carbon, High Chromium White Iron |
Alloy A49 is a corrosion resistant white iron suitable for low pH corrosion duties, where erosive wear is also a problem. The alloy is particularly suitable for Flu Gas Desulphurisation (FGD) and other corrosive applications, where the pH is less than 4. The alloy can also be used in other mildly acidic environments. A49 has an erosion resistance similar to that of Ni-Hard 1. |
A51 | ULTRACHOME 36% Cr, Low C | Erosion/ Corrosion White Iron | ULTRACHOME A51 is a premium erosion/corrosion alloy to be used where excellent erosion and corrosion resistance is required. The alloy has much improved corrosion resistance compared to alloy A49, whilst the erosion resistance is similar to Ni-Hard type alloy irons. The alloy is suitable for phosphoric acid duties, FGD duties, sulphuric acid , and other moderately corrosive applications. |
C02 | Ni-Resist (Copper free) | Corrosion Resistant Cast | Alloy C02 is a high nickel cast iron useful for light chemical duties involving low |
WARMAN CODE | MATERIAL NAME | TYPE | DESCRIPTION |
Iron | concentration of solids. | ||
C14 |
27 Cr-0.4 C5 Stainless Steel |
Duplex Stainless Steel | Alloy C14 is a corrosion resistant stainless steel suitable for use in acidic environments. The alloy is particularly suitable for Flue Gas Desulphurisation (FGD) applications, where the pH is between 3 and 7. The alloy offers moderate erosion-corrosion resistance. |
C21 | Type 420C Stainless Steel | Martensitic Stainless Steel | Alloy C21 is a martensitic stainless steel having a combination of high hardness and good general corrosion resistance. The alloy is machined in the annealed, or as cast condition and is subsequently hardened for service. |
C23 | Type 316 Stainless Steel | Austenitic Stainless Steel | Alloy 23 (316SS) is an austenitic stainless steel having excellent corrosion resistance in reducing media. The molybdenum present in C23 increases its resistance to pitting corrosion. The alloy has good mechanical properties, however its low hardness gives it a low erosion resistance. |
C25 | Alloy 20 | Austenitic Stainless Steel | Alloy C25 was specifically developed for sulphuric acid applications. The alloy can be used successfully in up to 85% Sulphuric acid. Alloy C25 also offers excellent corrosion resistance to a wide range of acids, and some strong alkalies. The alloy has poor resistance to erosive wear. |
C26 | 26 Cr 5 Ni Stainless Steel (CD-4M Cu) | Duplex Stainless Steel | Alloy C26 is a corrosion resistant stainless steel suitable for use in acidic environments. The alloy offers moderate erosion-corrosion resistance. |
C27 | ‘825’ Alloy | Austenitic Corrosion Resistant Alloy | Alloy C27 is an austenitic corrosion resistant alloy suitable for strong acid duties. |
C30 | 27 Cr 31 Ni Stainless Steel | Austenitic Stainless Steel | Alloy C30 is an all purpose austenitic stainless alloy for service in high corrosive conditions. C30 has excellent resistance to general corrosion, pitting, crevice corrosion, intergranular corrosion and stress corrosion cracking. The alloy was developed originally for use in phosphoric acid. |
C44 | Type 440C Stainless Steel | Hardenable Stainless Steel | C44 is a martensitic stainless steel having a higher carbon level than 420C (C21) alloy. The higher carbon level results in |
WARMAN CODE | MATERIAL NAME | TYPE | DESCRIPTION |
the formation of carbides within the microstructure. These carbides give 440C an improved wear life under the conditions of abrasive wear, as experienced with shaft sleeves. The formation of the carbide results in a reduction of the corrosion resistance of C44, compared with C21. | |||
C55 | Ferralium 255 | Duplex Austenitic/ Ferritic Stainless Steel | Alloy C55 is a duplex ferritic – austenitic stainless steel. It combines high strength and physical properties with excellent corrosion resistance. Alloy C55 offers improved resistance to stress corrosion cracking, pitting and crevice corrosion over C22, C23 and C25 grades of stainless steel. |
D21 | Ductile Grey Iron (SG Iron) | Cast Iron | Alloy D21 is a ductile grade of grey iron used where higher physical properties and greater shock resistance are required compared to alloy G01 |
D81 | Zinc Plated D21 | Zinc Plated SG Iron | Alloy D81 is a zinc plated ductile iron which is used for duties where higher physical properties and greater shock resistance are required in comparison to G01. D21 has a better atmospheric corrosion resistance than D21. |
G01 | Grey Iron | Cast Iron | Alloy G01 is an inexpensive alloy used where high physical strength and erosion resistance are not required. |
J21 | Tungsten Carbide V21 coated C21 | Ceramic Coated Stainless Steel | J21 is a ceramic coating (V21) applied over a C21 substrate. The combination of these two materials provides high abrasive wear resistance together with high toughness. The tungsten carbide layer is deposited onto the C21 substrate using a special spray technique which yields minimal porosity and excellent interlayer adhesion. J21 is unaffected by differential thermal expansion and will not “spall”. |
J24 | Tungsten Carbide V21 coated C23 | Ceramic Coated Austenitic Stainless Steel | J24 consists of a V21 ceramic coating deposited onto a C23 substrate using a special spray technique. The coating is very hard and offers excellent abrasive wear resistance. The spray technique gives a coating with minimal porosity and excellent interlayer bond strength. J24 is unaffected by differential thermal expansion and will not “space”. |
J25 | Tungsten Carbide | Tungsten | J25 consists of V21 ceramic coating |
WARMAN CODE | MATERIAL NAME | TYPE | DESCRIPTION |
V21 Coated C11 | Carbide V21 Coated C11 | deposited onto a C21 substrate using a special spray technique. The coating is very hard and offers excellent abrasive wear resistance. The spray technique gives a coating with minimal porosity and excellent interlayer bond strength. J25 is unaffected by differential thermal expansion and will not “spall”. | |
J26 | Chrome Oxide (Y03) coated C26 | Ceramic Coated Stainless Steel | J26 consists of Y03 Ceramic Coating deposited onto a C26 substrate using a special spray technique. The coating is very hard and offers excellent abrasive wear resistance. The spray technique gives a coating with minimal porosity and excellent interlayer bond strength. J26 is unaffected by differential thermal expansion and will not spall. |
J27 | WC/Chromium/ Nickel Coated C26 | Tungsten Carbide V23 Coated C26 | J27 consists of a WC/Cr/Ni (V23) coating deposited onto a duplex stainless steel (C26) substrate using a thermal spray technique. The coating offers both abrasive wear resistance and corrosion resistance exhibiting minimal porosity. |
N02 | 63 Ni 30 Cu Alloy | Corrosion Resistant Alloy | Alloy N02 is a nickel based corrosion resistant alloy for use in reducing acids and chlorides. It is used extensively in pickling and marine applications. |
N04 |
58 Ni 16 Cr 16 Mo Alloy |
Corrosion Resistant Alloy | Alloy N04 is a nickel based corrosion resistant alloy specially resistant to oxidising acids and reducing chlorides based solutions. |
N05 | 55 Ni 22 Mo Alloy | Corrosion Resistant Alloy | Alloy N05 is a chemical resistant alloy which can be used in non-oxidising environments. It has high physical properties and can be used successfully in high temperature environments. |
N22 |
55 Ni 22 Cr 13 Mo Alloy |
Corrosion Resistant Alloy | Alloy N22 is a nickel based corrosion resistant alloy specially resistant to extreme oxidising acids and reducing chloride based solutions. Its resistance to pitting in these solutions is superior to that of N04 and N05. |
N23 |
55 Ni 22 Cr 13 Mo Alloy (Wrought) |
Hastelloy® C22 | Alloy N23 is a nickel based corrosion resistant alloy specially resistant to extreme oxidising acids and reducing chloride based solutions. Its resistance to pitting in these solutions is superior to that of N04 and N05. |
WARMAN CODE | MATERIAL NAME | TYPE | DESCRIPTION |
P09 | Polyester Fibreglass DMC | Reinforced Structural Polymer |
P09 is a reinforced polyester resin used for structural pump parts as a replacement for heavier grey and ductile iron parts. The combination of glass fibres and a crystalline resin provides a material with excellent mechanical properties. |
P50 |
Polyphenylene Sulphide (Ryton*) * Ryton is a trade name of the Phillips Chemical Company) |
Reinforced Structural Polymer | P50 is a high-strength plastic suitable for parts requiring high-dimensional stability. |
P60 | UHMW Polyethylene | Engineering Polymer | |
R08 | Standard Impeller Rubber | Natural Rubber | R08 is a black natural rubber, of low to medium hardness. R08 is used for impellers where superior erosive resistance is required in fine particle slurries. The hardness of R08 makes it more resistant to both chunking wear and dilation (ie, expansion caused by centrifugal forces) as compared to R26. R08 is generally only used for impellers. |
R24 | Anti Thermal Breakdown Rubber | Natural Rubber | Anti Thermal Breakdown Rubber (ATB) is a soft natural rubber based on R26, but with improved thermal conductivity. It is intended for use as a liner material in slurry pumping applications where high impeller peripheral speeds are required. |
R26 | Standard Liner Rubber | Natural Rubber | R26 is a black, soft natural rubber. It has superior erosion resistance to all other materials in fine particle slurry applications. The antioxidants and antidegradents used in R26 have been optimised to improve storage life and reduce degradation during use. The high erosion resistance of R26 is provided by the combination of its high resilience, high tensile strength and low short hardness. |
R33 | Natural Rubber – Reinforced | Natural Rubber | R33 is a premium grade material for use where R26 does not provide sufficient wear life. It is a black natural rubber, of low hardness and is used for cyclone and pump liners and impellers where its superior physical properties give increased cut resistance to hard, sharp slurries. |
WARMAN CODE | MATERIAL NAME | TYPE | DESCRIPTION |
R38 | Natural Rubber Reinforced | Natural Rubber | R38 is a black natural rubber, of medium hardness. R38 is used for impellers where superior erosive and tear resistance is required in fine particle slurries. The hardness and tear resistance of R38 makes it more resistant to both chunking wear and dilation (ie, expansion caused by centrifugal forces) as compared to R26 and R08. R38 is generally only used for impellers. |
R66 | 60 Duro Natural Rubber | Natural Rubber | This is a hard (60 Duro) natural rubber product used for FGD duties primarily in GSL Pumps. |
S01 | EPDM Elastomer | Synthetic Elastomer |
S01 is an acid and ozone resistant rubber which is of low abrasion resistance. EPDM is non polar and difficult to bond to metal, therefore it is used typically in lipseals and volute seal applications. |
S02 | EPDM General Rubber | Synthetic Elastomer | S02 is an acid and ozone resistant rubber which is of medium abrasion resistance. EPDM is non polar giving it special chemical resistance. S02 is a speciality elastomer for use only in applications that require the properties of EPDM. |
S03 | High Temperature EPDM | EPDM | S03 is a high temperature and chemical resistant EPDM elastomer. It has been compounded so as to have a very low compression set and is therefore designed for use in sealing applications. This material is not designed for general use in parts subjects to erosive wear. |
S12 | Nitrile Rubber | Synthetic Elastomer | Elastomer S12 is a synthetic rubber which is generally used in applications involving fats, oils and waxes. S12 has moderate erosion resistance. |
S21 | Butyl Rubber | Synthetic Elastomer | Butyl rubber is a highly saturated elastomer which has excellent chemical stability, and good resistance to heat and oxidation. The high saturation reduces the elastomeric properties of S21, and hence reduces its erosion resistance. In general S21 is used in acidic environments. |
S31 |
Chlorosulfonated Polyethylene (Hypalon*) * Hypalon is a trademark of the |
Synthetic Elastomer (CSM) | S31 is an oxidation and heat resistant Elastomer. It has a good balance of chemical resistance to both acids and hydrocarbons. |
WARMAN CODE | MATERIAL NAME | TYPE | DESCRIPTION |
Dupont Company | |||
S42 |
Polychloroprene (Neoprene*) * Neoprene is the trademark of the Dupont Company |
Synthetic Elastomer (CR) | Polychloroprene (Neoprene) is a high strength synthetic elastomer with dynamic properties only slightly inferior to natural rubber. It is less effected by temperature than natural rubber, and has excellent weathering and ozone resistance. It also exhibits excellent oil resistance. |
S45 | High Temperature Hydrocarbon Resistant Rubber | Synthetic Elastomer | S45 is an erosion resistant synthetic rubber with excellent chemical resistance to hydrocarbons at elevated temperatures. |
S51 |
Fluoroelastomer (Viton*) * Viton is the trademark of the Supon Company |
Synthetic Elastomer (FPM) |
S51 has exceptional resistance to oils and chemicals at elevated temperatures. Limited erosion resistance. |
U01 | Wear Resistant Polyurethane | Polyurethane Elastomer | U01 is an erosion resistant material that performs well in elastomer applications where ‘tramp’ is a problem. This is attributed to the high tear and tensile strength of U01. However, its general erosion resistance is inferior to that of natural rubber (R26, R08). |
Y07 | Alumina 99% | Ceramic | Wear resistant ceramic. |
Y08 | Silicon Nitride Bonded Silicon Carbide | Ceramic | Wear resistant ceramic. |
Y11 | Fine Grained SiN/SiC | Wear Resistant Ceramic | Y11 is produced by bonding a fine grained silicon carbide powder with silicon nitride. The ceramic has high thermal shock resistance and physical properties. Y11 has a high wear resistance, compressive strength and modulus of rupture than Y08. |
Y14 | Reaction Bonded Silicon Carbide | High Wear Resistant Ceramic | Y14 is produced by reaction bonding silicon carbide grains with silicon nitride. The ceramic has high thermal shock resistance and physical properties, high wear resistance and high corrosion resistance. Y14 can be manufactured in thin sections of 5mm up to approximately 25mm. |
Z11 | Material Composite Y11/U01 | Ceramic Polyurethane Combination |
Z11 is a useful material for applications requiring low angle erosion and abrasion resistance. The Y11 Silicon Nitride bonded Silicon Carbide tiles provide a |
WARMAN CODE | MATERIAL NAME | TYPE | DESCRIPTION |
very hard wear resistant surface with the U01 polyurethane providing support. The polyurethane backing allow the ‘brittle’ ceramic tile to float and absorb higher angle and large particle impacts. | |||
Z12 | Material Composite Y11/A12 | Ceramic Alloy Combination | Z12 is the combination of Y11 Nitride bonded Silicon Carbide and A12 Ultrachrome 27% Cr White Iron. It is application for parts that require resistance to low angle erosion and sliding abrasion for particle sizes up to 5mm. |
Z13 | Material Composite Y11/A05 | Ceramic Alloy Combination | Z13 is the combination of Y11 Nitrided bonded Silicon Carbide and A05 Ultrachrome 27% Cr White Iron. It is applicable for parts that require resistance to low angle erosion and sliding abrasion for particle sizes up to 5mm. |
Z14 | Reaction Bonded Silicon Carbide/Foam | Ceramic/ Polyurethane Foam Combination | Z14 is used in cyclone spigot liners. The ceramic Y14 is coated in polyurethane foam. This foam provides protection and a light weight coating to seat the thin walled ceramic in position in the DMC casing. |
Z15 | Nitride Bonded Silicon Carbide / Polyurethane | Ceramic / Polyurethane Combination | Z15 is a useful material for applications requiring low angle erosion and abrasion resistance. The Y08 Nitride bonded Silicon Carbide tiles provide a very hard, wear resistance surface with the U01 polyurethane providing support. The polyurethane backing allows the ‘brittle’ ceramic tile to float and absorb higher angle and large particle impacts. |
Z16 | Nitride Bonded Silicon Carbide / UltrachromeÔ 27% Cr | Ceramic / White Iron Combination | Z16 is the combination of Y08 Nitrided bonded Silicon Carbide and A05 UltrachromeÔ 27% Cr White Iron. It is applicable for parts that require resistance to low angle erosion and sliding abrasion for particle sizes up to 1000mm. |